Warehouses are essential parts of the supply chain that serve as product storage and distribution centers. They are responsible for ensuring that products are delivered to customers efficiently and on time. To achieve this, warehouse management staff must constantly optimize their operations, ensuring they use the available space effectively and maintain accurate inventory.
Strategies for Efficient Inventory Handling
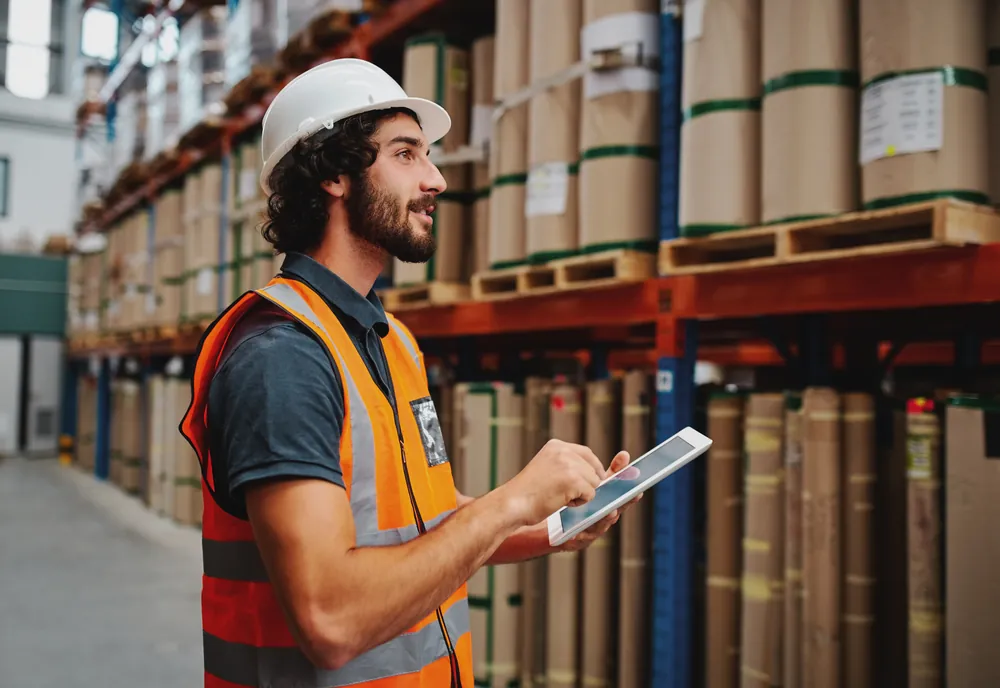
Warehouse Management Systems (WMS) are software applications that help warehouse management staff achieve these goals by providing real-time data on inventory levels, tracking product movement, and automating various warehouse management processes. Using WMS, managers can make better-informed decisions and improve overall warehouse performance.
Warehouse Layout Optimization
Flow Design: By arranging the warehouse logically, products can be moved seamlessly from the receiving area to storage and shipping. This avoids congestion and delays in the movement of goods.
Zone Picking: Organizing the warehouse into specific zones, with each area assigned to particular products, can reduce worker travel time and boost productivity. Workers can focus on picking and packing products in their trusted zone without having to traverse the entire facility.
Vertical Space: Effective use of vertical space is a key consideration in any warehouse layout. By using tall shelving and racks, it’s possible to maximize storage capacity without taking up additional floor space. This can be particularly valuable in high-density storage environments where area is at a premium.
Space Utilization
Slotting Optimization: This involves reviewing and updating the arrangement of products within the warehouse to improve access to fast-moving items. By placing popular items closer to the shipping area, workers can more quickly and easily retrieve them, saving time and reducing errors. This process should be done regularly to optimize the warehouse managment for maximum efficiency.
Pallet Racking: Investing in pallet racking systems is a smart way to maximize vertical space in the warehouse. These systems allow for efficient stacking and retrieval of pallets, which can help reduce the floor space needed to store products. Additionally, pallet racking systems can be customized to fit the specific needs of each warehouse, making them a versatile option for any business.
Bulk Storage: Items with low turnover rates can take up valuable space in high-traffic warehouse areas. You can free up space for more frequently used products by designating a bulk storage area for these items. This area should be easily accessible but not impede traffic flow within the warehouse.
By implementing these detailed ideas, warehouse managment staff can optimize their use of space and improve overall efficiency, leading to increased profitability and customer satisfaction.
Inventory Control
Cycle Counting: Regularly perform cycle counts to identify and correct discrepancies immediately.
ABC Analysis: Categorize your products into A, B, and C groups based on their importance. Focus on tracking your A items accurately.
Just-In-Time (JIT) Inventory: Consider implementing JIT practices to reduce excess stock and storage costs. This will help you maintain only the inventory levels required for your business operations.
Warehouse Management Systems (WMS)
Automation: One of the primary benefits of a WMS is automation. It streamlines essential tasks such as order processing and inventory tracking. Automating these processes can significantly reduce human errors, saving you time, money, and headaches.
Real-Time Tracking: A WMS provides real-time visibility into your inventory levels, order status, and worker performance. You can track your inventory levels in real-time, ensuring you always have the right products in stock. You can also monitor order status, which helps you identify bottlenecks and take prompt action to resolve them. Additionally, you can track worker performance, which enables you to identify areas where you can improve productivity.
Optimized Picking: A WMS can optimize your picking process by suggesting the most efficient picking routes. It can consider factors such as the location of products, the size of the order, and the availability of workers to recommend the best way. This can save you time and reduce labor costs, leading to increased productivity and faster order fulfillment. Additionally, it can help you deliver products to your customers faster, improving customer satisfaction.
Implementing a WMS can provide several benefits, including automation, real-time tracking, and optimized picking. These benefits can help you streamline warehouse management operations, increase productivity, and improve customer satisfaction.
Warehouse Management Staff
Training: Regular training sessions should be provided to your staff to ensure they are up-to-date on the latest best practices and safety procedures. This will help them perform their duties effectively while ensuring they always remain safe.
Performance Metrics: Evaluating employee productivity using performance metrics effectively ensures your staff performs to the best of their abilities. This will help you to identify areas where improvements can be made and provide constructive feedback to your team.
Task Assignment: Assigning tasks based on each worker’s strengths is a great way to optimize productivity. This will ensure that staff members work in areas where they are most effective, which will help to improve their job satisfaction and motivation.
Demand Forecasting and Order Fulfillment
Another crucial aspect of demand forecasting is collaboration. Businesses must work closely with their suppliers to ensure timely replenishment of inventory. This will help prevent stockouts and ensure enough list is available to meet customer demand. When suppliers are involved in the forecasting process, they can help provide more accurate information about lead times and delivery times, which will help businesses plan their inventory levels more effectively.
Order batching is another technique that can be used to improve efficiency in inventory warehouse management. By grouping orders, businesses can reduce the number of picking trips needed, which can help to save time and reduce labor costs. This technique is beneficial for companies that deal with a high volume of orders, as it allows them to streamline their operations and reduce the number of errors in the order fulfillment process.
Accurate demand forecasting is crucial for any business that manages an inventory of goods or products. Companies can optimize inventory levels, reduce costs, and improve customer satisfaction by analyzing historical sales data, collaborating with suppliers, and using techniques like order batching.
Improving warehouse management efficiency is an ongoing process that requires careful planning, organization, and modern technology like Warehouse Management Systems. By optimizing your warehouse layout, maximizing space utilization, implementing effective inventory control strategies, and focusing on staff management, demand forecasting, and order fulfillment, you can ensure that your warehouse management operates at its highest potential, resulting in cost savings and better customer satisfaction. Start implementing these tips today to boost your warehouse’s efficiency and success.
Partnering for Warehouse Managment Excellence